
Punching special and according to standard
KACO’s stamping department, with its qualified employees, has acquired excellent skills as an internal supplier. Quality and safety are always in the foreground.
We support customers with the development, design and manufacture with the help of progressive and transfer tools as well as with combined tools, such as cut-pull-hole tools. Our particular strength lies in the production of rotationally symmetrical parts. These tools are used in our own punching shop on modern mechanical presses. To ensure optimum process monitoring, the department is equipped with all the necessary measuring and testing equipment.
As a matter of principle, the standards common in the automotive supply world are taken into account throughout the entire process chain. In addition, we seek solutions for customer-specific special requirements.
Our machine park in the stamping shop is excellently equipped. This includes automatic punching machines with press forces between 500 KN and 2000 KN and table lengths of up to 2000 mm. We also use progressive and transfer tools.

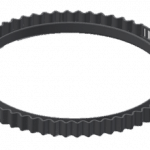
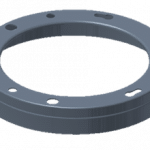
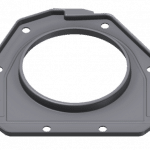
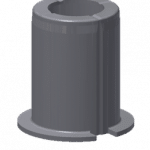
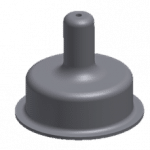
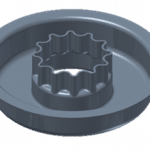
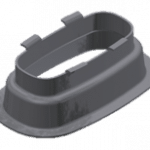
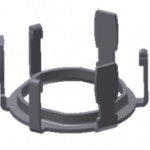
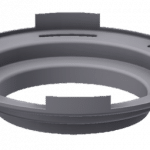
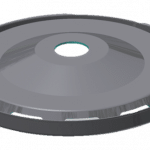
Quality through organisation
The success of the KACO stamping plant is based on many factors. The daily exchange of information between qualified employees via the shop floor, short decision-making processes and a high degree of flexibility make a significant contribution to the high level of quality. The high level of customer satisfaction is generated, among other things, by process monitoring through worker self-testing via the CAQ system and maintenance for mechanics, electrics and tools that accompanies production.
The tools themselves include complete cutting tools, progressive dies and transfer tools. In the area of forming, the range of articles extends from 6 mm to 200 mm diameter, a material thickness of 0.3 mm to 2 mm and a drawing height of up to 50 mm.
